Your Guide to Oil and Gas Corrosion Control
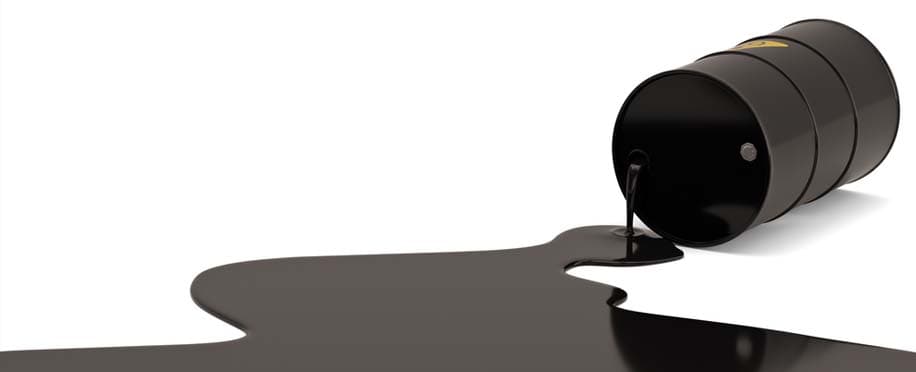
Posted on : 11/27/2022, 6:27:14 PM
To ensure a steady flow of oil and gas to consumers, field operators and line engineers must be adequately aware of oil and gas corrosion control because lines and their equipment will undoubtedly be prone to degradation due to erosion. This article provides an overview of all the information they need on gas and oil erosion and how to reduce and mitigate their damage.
What is the concept of corrosion in oil and gas?
Corrosion is a natural phenomenon resulting in a devastating change in petroleum pipeline metals, oilfield equipment, gas processing units, and refineries from valves, reservoirs, and other special equipment in the production process and as a result of an electrochemical or chemical reaction between the metal and its immediate surrounding environment, resulting in a change in mineral properties and weakening.
Corrosion is one of the critical topics to discuss because it is inevitable due to the material's innate desire to reduce the energy of Gibbs; all materials, in general, seek to achieve the lowest energy condition to reach the state of low energy oxide. While this is the natural state of all materials, it is necessary to consider how to balance materials and their surrounding environment to control corrosion in oil and gas.
Modern corrosion seeks to achieve that balance and has roots in electrical chemistry and metal science fundamentals. Electrical chemistry helps to increase understanding of the nature of materials through corrosion; metallurgy provides all information on materials, their alloys, and behaviour and thus offers a way to reduce their deterioration to maintain the general safety of facilities and reduce the high cost of large-scale maintenance.
It also controls the corrosion mechanism and its development speed in the environment where corrosion occurs, whether earthy, water, air, or other. Some settings can be an enabler of corrosion reduction, but others can be accelerated, and tailings and industrial products either stimulate or discourage corrosion.
What are the most common types of corrosion in oil and gas?
The crude oil and natural gas industry includes the following essential types of corrosion:
- Galvanised corrosion: Galvanic corrosion occurs when two different metals are electrically collected when the minerals are electrified or when the minerals are electrically connected.
- Regular corrosion: This form of corrosion on pipes and equipment appears uniformly when exposed to the surrounding environmental conditions, as rust on the entire pieces and pipes appears regularly and uniformly.
- Corrosion pitting: in this case, corrosion appears in the form of drilling and stains on the metal, which indicates the exposure of that area to fracture in it or the protective layer, a form of topical corrosion.
- Cracking stress erosion: The expansion of crack structure within a corrosive environment can lead to sudden and unexpected failure of specially stress-prone metal alloys presenting at high temperatures.
- Water erosion: an electrochemical reaction of substances of their presence in wet-nature environments, such as sea lines in waters across oceans, resulting in deterioration in the metal's nature and vital characteristics.
How to control corrosion in oil and gas?
To reduce and control corrosion problems, action must be taken in the oil and gas industry to increase the operating life of the equipment and raise production efficiency. In some cases, erosion is imperative and cannot be stopped. Still, a range of methods and techniques can be applied to reduce it and prevent its spread, including:
- Rust and oxidation:
Rust is often destructive in some cases; it is the solution to corrosion control in gas and oil pipes.
Especially since technically rust is iron oxide, when the surface of ferrous or steel pipes leaves exposed to the outdoors, it will rust rapidly. Still, with the thickening of the rust layer, the oxidation rate decreases, and that layer eventually turns into a protective layer, this technique benefits in dry climates.
These technologies can also be used on equipment, copper pipe, aluminium, and other non-ferrous metals.
- Coverage and coating:
Covering different parts with a coat of paint improves the corrosion rate, so other tanks, pipes, and equipment must be kept painted. Often during the periodic maintenance of installations, indoor colouring within gas and oil transmission lines and storage tanks, in some cases, better prevent some types of corrosion.
Some parts do not need paint, such as stainless steel equipment, galvanised steel, and nickel-coated lines; oil protects the inner interests of pipes, equipment, and reservoirs from corrosion as long as it is not corrosive material.
- Use of corrosion-resistant materials:
Although most of the fittings and pipes in oil and gas plants are made of steel, some other materials that are less prone to corrosion, such as glass fibres that have recently been commonly used by oil and gas refiners, especially in the oil tank industry, can be used to avoid corrosive chemical reactions.
We can use stainless steel or nickel-coated equipment and some plastic materials in highly corrosive cases, such as polyvinyl chloride and polyethene.
Some other ways to prevent corrosion:
In cases where previous methods do not help mitigate the corrosion rate, some crucial chemicals can be used to achieve this; these are often expensive but very effective.
Other simple methods include removing wet dirt from around pipes and equipment to significantly reduce oxidation and electrochemical corrosion or wrapping underground buried lines with bitumen and rolling them to prevent moisture.
How to prevent electrochemical corrosion?
Electrochemical corrosion occurs due to the passage of a current resulting in a chemical reaction. The chemical response pulls electrons from the metal in one place. It deposits them elsewhere, producing a weakness in the properties of the material made of the metal in the area from which the electrons were withdrawn.
The current passed is either natural due to the wind producing, for example, static electricity, or an abnormal cause such as poor grounding or electrical leakage.
In this case, where the used flanged edges isolate the lines, which hampers the flow of electricity, melting elevators (anodes) also use protection. The anode is a column of negative nature that tends to lose electrons; these columns are based on releasing electrons instead of metal; the anode tube eats little by losing electrons, while the metal stays intact.
In some cases, power is itself a means of protection. For example, operators drill a shallow well with sacrificial anodes near the natural well from which oil or gas is extracted. These wells are called cathodic protection wells. These wells send small electric currents to the well and then return them within an electric circuit to the well's nozzle.
If you are an engineer, engineering student, or an oil and gas exploration and processing worker who needs training and a greater understanding of the basics of corrosion and mitigation, now enrol in a corrosion control course in the corrosion Control Oil and Gas Exploration Industry that our official website is honoured to offer to you.