Gas Lift vs. Other Artificial Lift Methods: Which Is Right for Your Well?
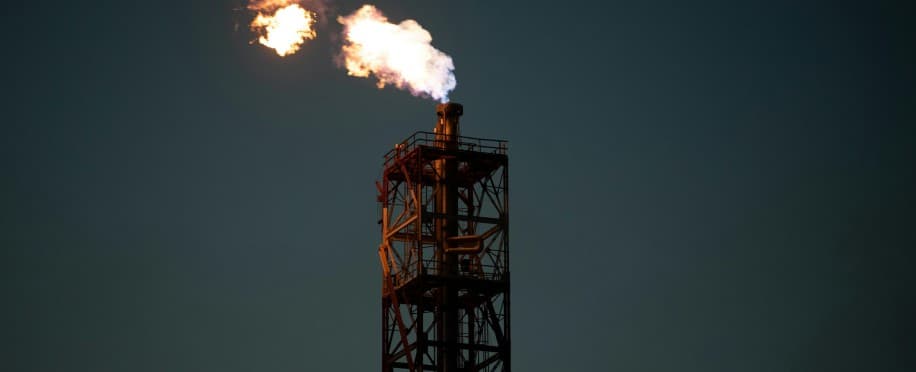
Gas Lift vs. Other Artificial Lift Methods: Which Is Right for Your Well?
Posted on : 4/16/2025, 9:09:17 PM
Gas Lift is one of the most commonly used artificial lift methods in oil and gas wells when natural pressure is no longer enough to support production. While this simple system has been a standard for decades across various fields and environments, many professionals still raise questions on how it compares to other lift techniques and whether it’s the right solution for their needs, infrastructure, and business goals.
In this article, we will explore gas lift systems in detail, compare them to other artificial lift options, and explain how to decide which lift method is suitable for your oilfield based on practical and operational conditions in the USA.
What Is Gas Lift and How Does It Work?
Gas lift is one of the most flexible and reliable lift solutions used in the field, especially when terrain, conditions, and production goals vary across locations. It involves injecting high-pressure gas, either compressed from an external source or produced onsite, into the casing of a well. This process reduces the density of the fluid column, allowing natural reservoir pressure to raise the fluids to the surface.
Once injected, the gas enters the tubing through a series of valves installed inside mandrels. These valves are designed to open at specific depths and outlet pressures. As the gas mixes with the liquid, small bubbles form and reduce fluid weight. This lifting effect allows for smoother pumping and easier fluid movement.
As the geotechnical engineering experts state, there are two primary gas lift models:
- Continuous gas lift, which is set for steady flow
- Intermittent gas lift, which operates in timed bursts to handle lower volumes or high-GOR fluids
Most of the equipment, such as compressors, controllers, and tubing packages, sit at the surface, making it easier to monitor and maintain. Gas lift does not require a downhole pump, and that makes it suitable for rough terrain and wells requiring frequent analysis, innovation, or quick field service.
When Should You Use a Gas Lift?
Gas lift is especially suitable for wells that produce mixed fluids, encounter scale, or experience variable pressure over time. It reduces maintenance needs, avoids rod wear, and supports production in challenging conditions.
This system works efficiently in both vertical and deviated wells and supports coiled tubing installations during completion. It is also highly compatible with automated tools and hpgl systems for performance tracking, dual output, and operational adaptability. Whether you’re starting new or supplementing an existing method, gas lift offers a seamless way to adjust for pressure drops, volumes, and flow uncertainty.
In areas like Midland, TX, where wells are spread across wide fields and service logistics matter, gas lift becomes more than a lift strategy—it becomes an operational solution.

How Gas Lift Compares to Other Artificial Lift Systems
As we’ve mentioned before, companies always ask what makes gas lifts different from other lift systems. Which ones to use and more, let’s take a closer look at the differences:
Electric Submersible Pumps (ESPs)
ESPs are commonly used in high-output wells. These units are driven by horsepower and require an electric source to operate at depth. However, these systems involve sensitive internal components, which makes them more likely to fail in harsh environments or when dealing with gases, sand, or rapid flow variation.
While ESPs can increase production when conditions are stable, they struggle with scaling, water-heavy fluids, and unpredictable terrain. They also require high stock levels, consistent surface power, and technical support, which adds to overall operating costs.
Rod Pumps and Hydraulic Systems
Rod pumps are well-known in shallow fields. They are often installed with scissor stands, mounts, and counterweight frames. But in deeper wells, the elevation pressure and flow inconsistency limit their performance. Hydraulic systems, meanwhile, involve pumping fluid to move a piston—an approach that needs stable water injection, smooth outlet flow, and high-precision monitoring. These are best reserved for custom applications with set conditions.
Gas lift, by comparison, offers a flexible and more forgiving design that fits into both turnkey and adjustable models. You can easily introduce it in existing completions or integrate it with hyrate gas compression for added efficiency.
As the International Energy Agency continues to guide global energy policies, many operators are re-evaluating lift strategies not just for performance but for sustainability, adaptability, and future-focused results.
What to Consider Before Making a Decision?
Choosing the right artificial lift method is a process that includes technical design, well analysis, field behavior, and completion goals.
Before you make a decision, ask:
- What type of formation are you operating in, and at what depth?
- Are you producing gas-heavy or liquid-rich streams?
- Can you access surface compressors, air units, and monitoring tools?
- Do you need a solution that fits across multiple wells or locations?
- Is your knowledge enough? Or should you consider Oil and gas courses in London to deepen your understanding?
Also, consider if you require something more flexible, such as a system that supports adjustable rates, fits into dual-well systems, or can operate seamlessly alongside other lift services.
Gas lift has a long history of success, particularly in complex environments, and it’s often selected because of its ability to reduce operational downtime, simplify maintenance, and support innovation.
Eventually,
Artificial lift is not just a well process—it’s a complete operational strategy that involves tools, packages, field services, and long-term planning. From the arm of your desk to the seat of a field chair, every engineer must consider how the lift system supports daily output, service uptime, and lifecycle cost.
Gas lift has been featured in countless completion designs and is often integrated into high-efficiency models with built-in monitoring. It’s easy to install, compatible with different production classes, and flexible enough to fit various conditions.
From wells operating in LP zones to lift systems built to maximize uptime and performance, gas lift remains one of the most trusted, scalable, and field-tested solutions in today’s energy arena. Whether you’re designing from scratch or improving your current system, gas lift can fit your base, support your structure, and help your production stand strong—day after day, across every elevation.