Mastering Precision: Top Quality Control Techniques for Enhanced Product Reliability
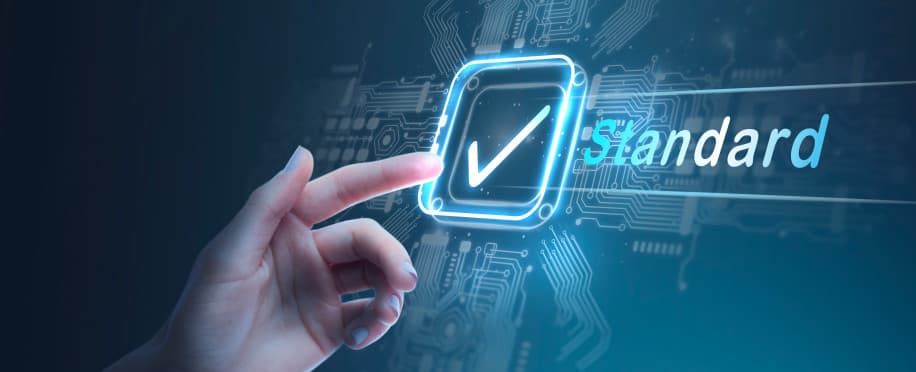
Mastering Precision: Top Quality Control Techniques for Enhanced Product Reliability
Posted on : 12/10/2023, 10:26:35 PM
Offering stable, high-quality services and products is critical in gaining customers and turning them into regulars without any issues; thus, monitoring your business’s quality control techniques and practices is your only way to ensure excellent quality.
Moreover, although there are different applied quality control types to follow, they all work toward the same goal of helping companies reach the best level of quality in all services or products.
This article will share insightful information about quality control techniques, including the main rules and the best procedures to follow in your QC strategy.
What Are Quality Control Techniques?
Quality control techniques are systematic processes, benchmarks, and methodologies to ensure that existing products or services meet the specified standards consistently.
Moreover, effective working to develop an effective quality system (QMS) should be done by identifying and correcting defects or deviations from quality standards throughout the production or service delivery life cycle.
Quality control techniques enhance outcome reliability, boost customer satisfaction, and fulfil the organisational development plan.
What Are the 4 Common Rules of Quality Control?
There are defined rules to follow in quality control techniques that will help and boost your quality management process to reach the highest level of effectiveness:
1. Check Each Stage:
Do not ignore any control stage, even if it is a minor and short procedure, as you must check and inspect each stage you perform without skipping.
2. Ensure Visibility:
Your employees and managers should see all the working stages and statistical numbers, even in other departments, as this standard rule could help them improve their working strategy and share suggestions to improve other departments.
3. Predict and Analyse:
Always predict possible risks and study your available information to set the best way for your quality control techniques based on accurate measurement.
4. Continuous Improvement:
The importance of technology quality improvement is undiscussable as it helps you determine your work effectiveness and ensures you the best quality level on all ongoing operations and systems in your project.
The 6 Cited Quality Control Techniques:
Each one of the quality control techniques offers a unique and oriented tactic for maintaining and upgrading product or service quality.
Moreover, the shared statistical numbers are all positive; thus, the choice of control technique depends on factors such as the nature of the industry, the scale of production, and the specific quality control requirements of the product or service.
1. 100% Inspection Method:
This quality control (QC) technique involves testing each process or product to ensure it is manufactured flawlessly and meets the required quality standards.
However, this quality management can be time-consuming and may not provide a practical solution for large-scale production programs.
2. Taguchi Method:
Named after the Japanese engineer Genichi Taguchi, this theory shows robust design to improve product quality and reduce variation by conducting analytical design experiments to optimise processes and enhance reliability.
3. X-Bar Chart:
Part of statistical process control, the X-Bar Chart monitors a process's central tendency (mean) over time to classify shifts or trends in data, enabling timely corrective actions and maintaining consistent quality.
4. Statistical Sampling:
This quality management process involves randomly selecting a subset (sample) of products or tools for inspection rather than examining every item.
Moreover, the statistical sampling procedure provides a cost-effective way to assess the quality of an entire batch or manufacturing run.
5. Six Sigma:
Six Sigma is a comprehensive quality control (QC) operation focused on minimising flaws and improving process efficiency.
This quality planning process employs statistical analysis and DMAIC (Define, Measure, Analyse, Improve, Control) methodology to identify and remove variations that may lead to flaws.
6. Total Quality Management (TQM):
This organisational approach involves all management members and employees and continuously enhances processes, tools, and products.
More than that, this quality management control is established by fostering a culture of quality, client satisfaction, and employee involvement to ensure sustained excellence.
Why Do You Need Quality Assurance Online Courses?
By investing in quality assurance online courses, you will gain new knowledge, skills, and mindset and guarantee positive impacts on your business’s reputation and competitiveness in the market.
- Gain industry-relevant skills, knowledge, the latest tools, and methodologies for quality assurance, ensuring that you are proficient in enhancing manufacturing reliability.
- Online courses in quality assurance often highlight international quality standards and compliance needs to help you meet the regulations in different markets and enhance the reliability of your activities.
- Quality assurance is a dynamic field with evolving technologies and tools; thus, continuous learning is essential to stay up-to-date on industry trends, emerging technologies, and new approaches to quality management.
- Learn efficient problem-solving methods, including root cause analysis, corrective action implementation, and techniques to minimise the impact on procedures reliability and prevent recurring problems.
Finally,
Learning about the best quality control techniques is the best way to establish the best quality planning for your business based on your needs and requirements.
Thus, you must invest in the latest technologies and training for your teams.